Occupational Health and Safety
Purpose
Ensure safe working conditions at all TMK enterprises for each employee and full employee compliance with occupational health and safety requirements.
Zero injuries is a key goal of the Company’s 2027 development strategy.
Governing regulations
- Occupational Health and Industrial Safety Policy and Industrial Safety Policy
- OHSAS 18001 — Occupational Health and Safety Management System
- Regulations on the Occupational Health and Industrial Safety Contest for TMK Group Entities
- Occupational health and safety management system, including internal procedures aligned with applicable laws and international standards
Organization
Technical Director is responsible for organizing activities and achieving occupational safety targets at all TMK entities, with their KPIs including occupational health and industrial safety metrics. The occupational health and safety management system in place at all the Company’s enterprises includes regular assessment of occupational risks, special assessment of working conditions, workplace microclimate control measures, monitoring employee health, training and certifying employees in occupational health and safety.
Control
The Board of Directors, TMK’s executive management, Technical Director jointly with facility management.
TMK enterprises have been successfully certified to ISO 45001:2018
100% of production sites took part in Steel Safety Day 2020
LTIFR reduced to 0.21, hitting 4-year lows
Accident frequency rate decreased by 28%
The number of severe workplace injuries decreased by 25%
Emergency-free production
Decreasing number and frequency of accidents and the lost workday rate
Training and Education
OHS training at the Company meets the requirements of Russian federal laws and regulations on occupational health and safety. TMK2U Corporate University, in cooperation with the management company’s Occupational Health Department
- started training in Occupational Health and Safety for Managers and Specialists, First Aid, and Minimum Fire Technical Standards programs, involving external experts, for 230 employees of the management company
- develops a range of unique e-learning courses in Occupational Health and Safety for Managers and Specialists, Induction Briefing, Minimum Fire Technical Standards, Fire Safety Training, Training to Assign Group 1 on Electrical Safety to Non-Electrical Personnel, Occupational Risk Management. These programs are mandatory for all the Company employees
- regularly updates all developed courses in line with new statutory requirements to occupational health and safety.
In addition to mandatory training, TMK also provides training programmes and takes measures to improve the safety culture, personnel qualifications and competencies in occupational safety. For example, TMK2U Corporate University regularly offers e-learning courses, webinars and lectures on occupational health and technosphere safety, which were attended by 802 people in 2020.
The training extensively uses digital technology — for instance, Volzhsky Pipe Plant has a Steel Safety Room, demonstrating on a large screen production sites, hazards and occupational health techniques.
Volzhsky Pipe Plant also has a quest room with artificially created safety breaches. The employee in the room should identify and explain these breaches.
Supported by the corporate communications function and the corporate media, the Company actively promotes occupational safety, including engaging employees in occupational health and safety events and informing on preparing to, and holding of, Steel Safety Day.
Pursuant to the Regulations on the Occupational Health and Industrial Safety Contest for TMK Group Entities approved by the CEO’s directive, TMK holds a competition to select the organization with the best OHS performance, with Sinarsky Pipe Plant named the winner in 2020.
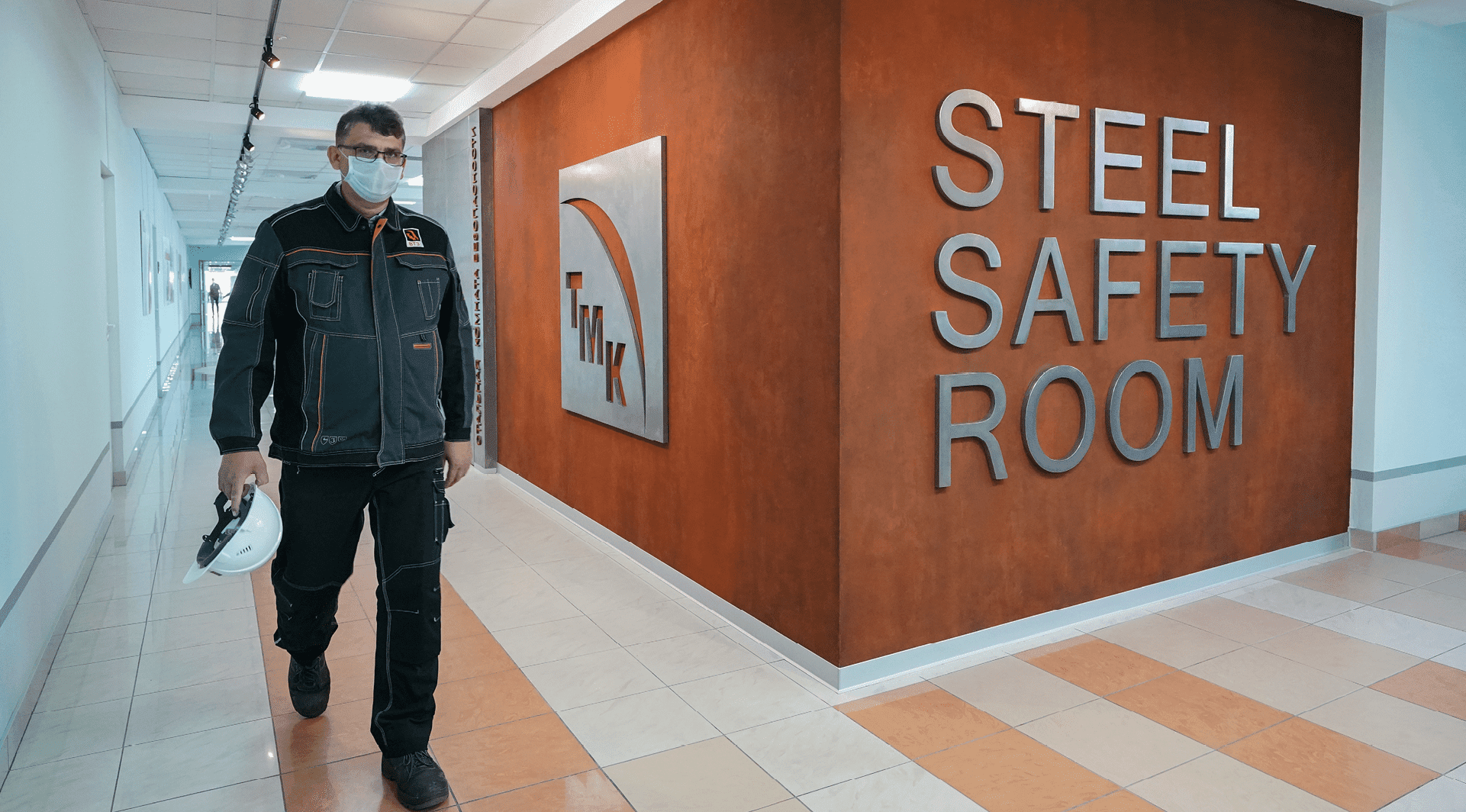
Risk Identification and Safe Environment
All TMK Group entities apply a risk-based approach and regularly review their occupational health and safety requirements in place, which are mandatory for all employees.
The key to improving safety is employee engagement. To date, about 80% of TMK Group employees are involved in identifying and eliminating risks. In February 2020, enterprises introduced hazard maps, which were drawn up with the help of employees. Hazard maps present a list of workplace hazards where risks cannot be completely eliminated, but can be controlled. During the year, the Company held briefings to employees on safety precautions based on the risks identified, and installed barriers and other security equipment to ensure maximum injury protection.
The enterprises continuously monitor the working environment as per schedules, which enables real-time employee risk assessment and prompt organizational and technical measures to eliminate or reduce the impact of risks.
In line with tradition, all TMK Group production facilities as well as contractor employees took part in Steel Safety Day 2020. The results were summarized in October 2020 instead of the World Day for Safety and Health at Work on April 28 due to the COVID-19 pandemic and submitted to the World Steel Association. During the year, the Company followed the plan to eliminate or mitigate the identified safety risks. All of the plan’s activities are running to schedule.
Participants | 2018 | 2019 | 2020 |
---|---|---|---|
TMK employees | 35,518 | 35,962 | 31,821The number of participating employees decreased due to the sale of the American division. |
Including safety auditors, % | 81 | 81 | 83 |
Contractor employees | 6,924 | 7,350 | 7,611 |
In 2020, RUB 770 million was allocated to occupational health and safety, up 30% year-on-year.
The most significant activities to enhance occupational safety at the Group entities include
- certification to ISO 45001
- pilot corporate electronic health check system at TAGMET launched in 2019. Digital tools enable automated health screening to identify alcohol and drug use. During the year, “Electronic” health checks were rolled out to four more TMK plants: Seversky Pipe Plant, Volzhsky Pipe Plant, Sinarsky Pipe Plant and Orsky Machine Building Plant
- targeted inspections to mitigate safety risks related to moving parts and machinery
- targeted inspections and follow-up installation of barriers and lockouts to prevent entry into areas with operating equipment
- firefighting equipment serviceability checks in October and December 2020
- further rolling out best practices at enterprises, including in process digitization:
— Participation in BIOT (Safety and Labor Protection) interactive exhibition
— Exchange of best practices in occupational health and safety between heads of technical services and departments of TMK’s Russian division, representatives of United Metallurgical Company (OMK), Chelpipe Group, the State Labor Inspectorate of the Volgograd Region, and the Nizhne-Volzhsky Department of the Federal Environmental, Industrial and Nuclear Supervision Service (Rostechnadzor)
— Online meetings with heads of OHS organizations, including meeting dedicated to implementing digital technologies
— Participation in expert groups of the Russian Union of Industrialists and Entrepreneurs (RSPP) to improve applicable health and safety laws under the governmental regulatory guillotine policy
- installation of video surveillance at enterprises to ensure compliance with safety requirements and assist in accident investigations.
Ensuring Employee Health and Safety During the COVID-19 Pandemic
Throughout 2020, TMK strictly complied with the recommendations of federal and regional authorities and the Russian Federal Service for Surveillance on Consumer Rights Protection and Human Wellbeing (Rospotrebnadzor) to enforce hygiene safety and prevent the spread of COVID-19 at the Group’s production sites and offices.
The following measures were implemented during the reporting period:
- Floor markings to mark out social distancing of 1.5–2 meters
- One-way flows through the Group’s buildings and sites
- Mandatory use of provided protective equipment (respirators and hand protection) at all the Group’s premises
- Hand sanitizers to disinfect hands
- Thermal imaging cameras to screen body temperature at entrances to buildings, body temperature measurements during the day using digital thermometers
- Regular disinfection and installation of germicidal lamps in rooms
- Discouraging trips within buildings, face-to-face contacts, meetings in person; moving meetings and events online
- Partially shifting the Company employees to remote work, creating cross-platform mobile workspaces that are managed remotely
- Cancelling or postponing mass business, sporting and cultural events, banning business trips abroad
- Changing work and rest schedules (setting individual schedules, changing shift patterns) to minimize congestion in offices and reception areas
- Setting a timetable for visiting canteens and coffee shops
- Banning external meal delivery to offices
- All employees are strongly advised to self-isolate and follow other measures to counter the spread of COVID-19 as required by regional authorities.
PERFORMANCE INDICATORS
Indicator | 2018 | 2019 | 2020 |
---|---|---|---|
Accidents | 23 | 17 | 12 |
including fatalities | 0 | 0 | 1 |
Frequency rate | 0.68 | 0.5 | 0.36 |
Severity rate | 75.7 | 89.4 | 89.0 |
Lost workday rate (LWR = FR x SR) | 51.5 | 44.7 | 32.4 |
Indicator | 2018 | 2019 | 2020 |
---|---|---|---|
Accidents | 20 | 16 | 12 |
including fatalities | 0 | 0 | 1 |
Frequency rate | 0.63 | 0.51 | 0.38 |
Severity rate | 70.8 | 87.4 | 89.0 |
Lost workday rate (LWR = FR x SR) | 44.6 | 44.5 | 33.9 |
Indicator | 2018 | 2019 | 2020 |
---|---|---|---|
Accidents | 3 | 1 | 0 |
including fatalities | 0 | 0 | 0 |
Frequency rate | 1.33 | 0.87 | 0.0 |
Severity rate | 108.3 | 14.5 | 0.0 |
Lost workday rate (LWR = FR x SR) | 144.0 | 12.6 | 0.0 |
In 2020, the Company’s injury metrics have improved.
LTIFR reduced to 0.21, hitting 4-year lows, the accident frequency rate decreased by 28% year-on-year, the number of severe cases by 25% year-on-year, and the lost workday rate by 25.8% year-on-year. The Company’s management pays close attention to health of employees injured in accidents, monitoring their treatment, state and the quality of treatment.
The Company deeply regrets to report that one fatality was recorded at Volzhsky Pipe Plant in 2020. The incident was investigated to identify the causes, and measures were taken to prevent such incidents in the future.
2021 Plans:
- Digitization of occupational health and industrial safety services
- Integration of new companies joining TMK Group