Digital Transformation
In 2020, TMK’s digital transformation efforts were focused on the implementation and deployment of large-scale cross-functional solutions affecting various areas of the Company’s business.
The key area of TMK’s ambitious digitalization programme is embedding digital technologies in the operational management system. Our digital transformation journey is part of the wider TMK’s Digital Production program, which is aimed at driving the efficiency and quality of the operational management system covering production and production processes, including by improving planning to increase productivity, production rhythm and resource efficiency and hence contribute towards TMK’s strategic goals.
Digital transformation of production is based on a comprehensive solution and is driven by six interrelated projects covering all production processes: Manufacturing Execution System (MES) project, which includes major subsystems of operational production management across the Company’s plants, its functionality comprising the execution of core production operations, technical control (quality assurance) and inventory management; LIMS projects (laboratory testing), TORO (equipment maintenance and repair), ENERGY (energy resources), PIMS (storage and sharing of process and production data) and FLOW (product traceability at process level).
Execution of core production operations, technical control and inventory management
Energy management
Day-to-day laboratory information management
Data infrastructure creation
Management of equipment maintenance and repair
Product identification and traceability system
TMK’s Digital Production programme covers six enterprises (19 shops) of TMK’s Russian division: Volzhsky Pipe Plant, Seversky Pipe Plant, Sinarsky Pipe Plant, Taganrog Metallurgical Works (TAGMET), TMKCPW and TMK-INOX.
The first stage of TMK’s MES project involves a large-scale re-engineering of operational production management processes based on digital technologies and driven by maximized unification across all TMK enterprises. At its second stage, in 2022, the new MES system is expected to be deployed at pilot shops of participating enterprises, including Volzhsky Pipe Plant, Seversky Pipe Plant, Sinarsky Pipe Plant and TAGMET. During the final stage, the new system will be rolled out to the remaining shops as well as to TMK’s other facilities. The PSImetals solution by PSI, a German company specializing in software for the steel industry, was selected as the core technology platform to support our digitalization journey.
PIMS and TORO projects have piloted and tested new digital tools. We collate data about the operation of steelmaking units to implement their digital twins, which are the source of data for the MES system.
Projects to develop an industrial equipment monitoring system based on the Winnum digital information platform were implemented at TAGMET and Sinarsky Pipe Plant within the FLOW focus area. The implementation of the remaining modules — LIMS, ENERGY and FLOW — will start in 2021.
A great deal of preparatory work has been completed for the rollout of an Integrated Planning System (IPS). The large-scale project, launched in October 2019, aims to build a 1.5 year forward high-level sales and operations planning system (S&OP concept). It leverages the SAP IBP software solution as well as PSI tools to implement order portfolio management, as well as scheduling and master production scheduling at TMK plants. Once launched, the new software products will enable planning of optimal margins and capacity utilization based on reliable data and leveraging the most advanced analytical tools. The High-Level Planning (SAP IBP) and Order Portfolio and Technical Order Processing (PSI Metals) modules are scheduled for launch in the first half of 2021.
In spring 2020, TMK’s sales unit launched the Digital Heart of Sales project to implement a CRM system based on SAP Sales Cloud. The solution includes two modules: basic SAP C4C (to manage customer relationships) and SAP CPQ — product catalog configurator offering a toolkit to optimize pricing and quote management. The new products will be integrated into TMK’s existing information systems, enabling rapid sharing of data about customers, orders, production planning and shipments. In addition, the system will be synchronized with e-mail and TMK’s eTrade online store. The implementation of an advanced automated solution will open up new opportunities in customer relationship management, and enable the digitization and structuring of the sales planning and tracking process, converting it into a functional and flexible tool.
This solution, driven by an innovative software suite from SAP, is one of the first implementations in the CIS. The implementation process involves three stages, with stage one focused on the automation of business processes in domestic sales. Stage two will roll out the SAP Sales Cloud solution to the sales teams focused on domestic energy markets. Stage three will cover sales to overseas customers. The CRM system is scheduled to be fully launched into commercial operation by mid-2021.
An important milestone in TMK’s digitalization journey was the approval in June 2020 of TMK’s 2025 Digital Vision, which aims to widely implement Industry 4.0 digital technologies, and build a digital ecosystem with customers and suppliers, technology partners, universities and research groups to improve the quality and performance of products and services.
The implementation of initial digital initiatives has already shown results:
- A project to deploy robotic process automation (RPA) in market position analysis was completed;
- A recruitment software chatbot was launched to identify job seekers and handle CVs;
- A project to roll out an RPA software bot was completed in reconciliation management;
- Chatbot technology was piloted and tested in selected general and administrative processes at the management company.
TMK recognizes the value of big data-driven management decisionmaking and remains focused on driving internal efficiencies as part of its vision of becoming a data-drivenDriven by Big Data. company. A single platform for building a corporate data mart is being tested and selected, with several more initiatives in the pipeline.
TMK was the first company in Russia to launch an online tubular product store — TMK eTrade — in 2017. The launch of an additional, online sales channel has provided the Company with a global reach and strengthened its position in the spot market. At present, the entire range of products from TMK plants (Volzhsky Pipe Plant, Seversky Pipe Plant, TMK-CPW, TAGMET, Sinarsky Pipe Plant, TMK-INOX) can be purchased on the TMK eTrade platform, and orders can be placed for future pipe production.
The online store is constantly being improved, with additions to its toolkit and functionality. In 2020, an option was made available to Kazakhstan-based non-residents of Russia to purchase pipe from stock at TMK-Kazakhstan production site; the product offering was expanded with stainless steel pipe by TMK-INOX; the online store’s design was updated and a chatbot was deployed to advise users on a range of matters and, if necessary, pass on the chat to an appropriate Company employee; and the integration of the online store and the new CRM system in Sales is in progress.
In the reporting year, as part of the ongoing automation project covering existing business processes, we continued the transition to electronic document management (EDM), covering both external (suppliers and customers) and internal (plants exchanging documents on the domestic tubular product sales process) users. The COVID-19 pandemic has demonstrated the convenience and importance of promoting digital collaboration and building partner ecosystems. This process will gain further scale in 2021.
In 2020, TMK was one of the first companies in Russia to start the process of shifting its workforce to remote work amid the pandemic. The Company’s IT team deployed remotely controlled cross-platform mobile workstations for employees in the shortest possible timeframe — leveraging the previously implemented hybrid cloud-based data center. This has enabled a smooth transition with almost no interruption to business processes.
TMK’s project to set up cloud-based workstations for remote workers won the Project of the Year competition organized by the GlobalCIO | DigitalExperts professional community in the Cloud Environments category. The Project of the Year competition is held annually; projects compete in different categories grouped into three main areas: Best Domain-Specific Solution, Best Industry Solution and Best Management Project. Winners are selected through an independent online voting by members of the GlobalCIO | DigitalExperts professional community. Entries are assessed across a range of criteria including: scale, business impact, project complexity and optimal task match.
In the reporting year, the project to automate health checks, piloted at TAGMET in 2019, was moved forward. «Electronic» health checks were rolled out to four more TMK plants: Seversky Pipe Plant, Volzhsky Pipe Plant, Sinarsky Pipe Plant and Orsky Machine Building Plant.
In November 2020, TMK launched a new corporate website, the result of extensive modernization of the Company’s online presence drawing on state-of-the-art technology solutions.
In 2020, a joint project was also launched by TMK Group and Sinara Group to establish a Business Service Center in Yekaterinburg, LLC TsBU. The new structure will take over part of the business functions across the following areas: accounting, finance, HR management, legal support and information technology. The project has completed a diagnostic phase, mapping and analyzing the existing processes for each function and assessing the choice of solutions for effectiveness and efficiency. The diagnostic resulted in granular maps of business processes and an interaction map. Core IT solutions and platforms were also identified, and the development of regulatory documents and control environment was started for the service center.
The Company is working to transform its vast paper-based document flow into a single electronic archive. In 2020, the ECM systems were evaluated as part of the electronic archive implementation project, an IT system was selected, and an implementation contract was signed. A joint working group of TMK and Sinara Group kicked off the project’s system design stage. To ensure the effective management of services within the center, we plan to implement service management in accordance with the ITSM methodology and automate service delivery process using a service desk solution. At the end of 2020, eight systems were evaluated as part of a tendering process to select a service desk system. The winner was the Creatio system, a platform for business process management. The platform is expected to drive our digital transformation projects, including personal account, intranet portal, travel management, among others.
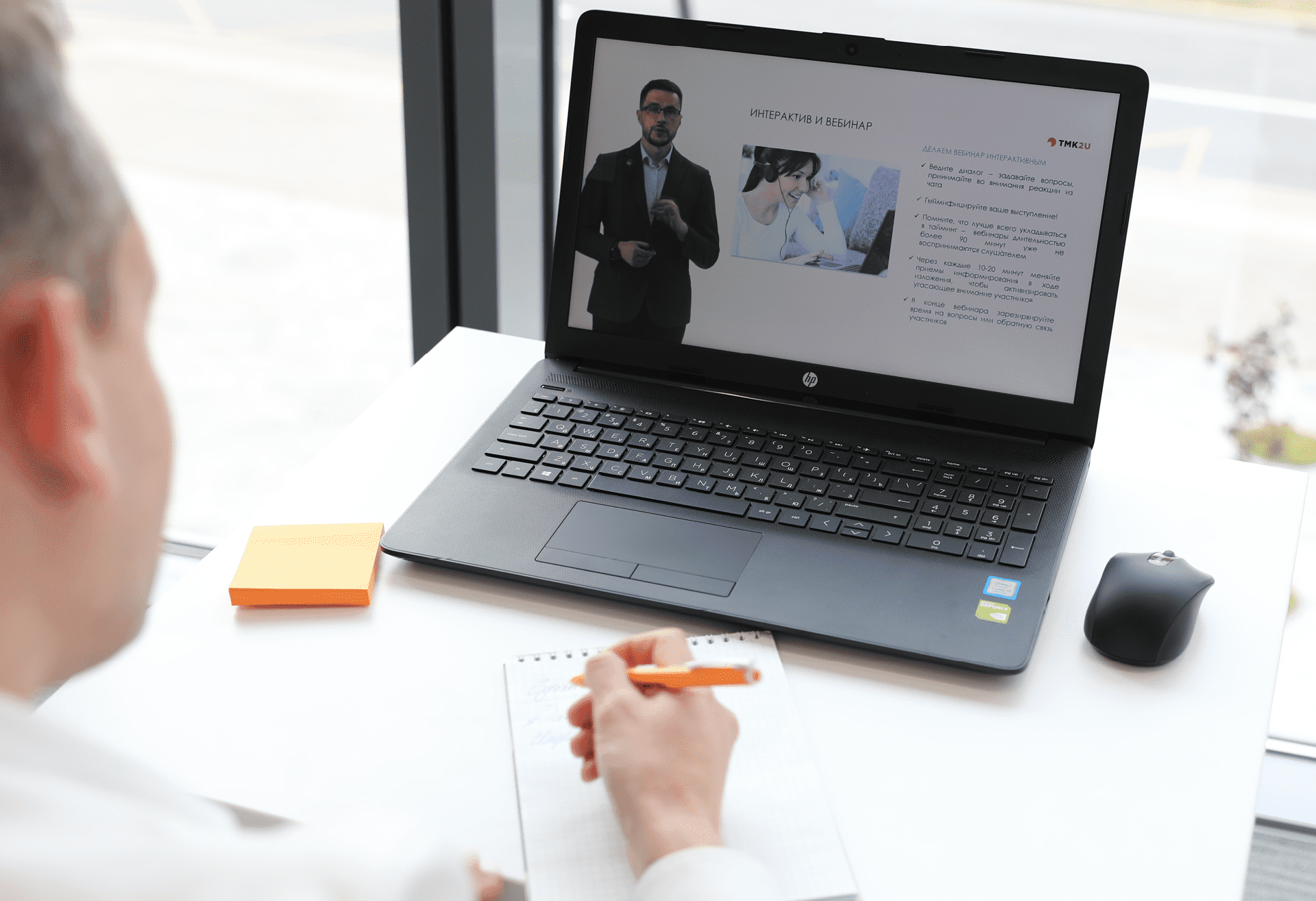