Innovation and R&D Cooperation
Deploying the latest technologies, the development and rollout of knowledge-intensive products and solutions, and rapid responses to new technology challenges, customer demands and preferences are all important drivers of the Company’s competitive edge in today’s global pipe market.
In 2020, TMK conducted research and development of new products at its own corporate centers: RUSNITI in Chelyabinsk and TMK’s R&D facility in Moscow’s Skolkovo Innovation Center.
This new TMK-owned R&D facility has become an important element of the Skolkovo Innovation Center ecosystem, offering unique professional development opportunities for a new generation of Russian engineers and researchers. For TMK’s R&D facility, 2020 was a period of building a research team, establishing ties with research organizations and teams of researchers and developers, mastering phase one’s set of unique equipment to both study structure and properties of materials, and to undertake full-scale research testing of new product samples made of them, as well as advancing projects in modeling and digitization of key production processes. The integrated capabilities of the corporate R&D facility in Skolkovo have helped to step up the development of new materials, designs and connection solutions for increasingly complicated hydrocarbon production conditions, as well as for other applications. In 2020, investments to complete and equip the center totaled more than RUB 300 million.
During the year, TMK’s R&D facility in Skolkovo successfully used its new unique equipment to conduct the first performance tests on two new TMK UP CENTUM and TMK UP MAGNA threaded connections for casing pipe. The reliability of these products under extreme conditions was confirmed by physically simulating the behavior of pipes with connections under high mechanical loads and elevated temperatures according to ISO 13679 and ISO 12835.
Joint research programmes between RUSNITI, TMK’s R&D facility in Skolkovo and TMK plants widely use the new capabilities of the laboratory equipment set, in particular, electron microscopy, physical and chemical analysis and mechanical properties analysis tools, to explore and develop new materials with increased strength and reliability, including special steels and alloys. This enables addressing complex tasks throughout the entire value chain, from the development and testing of new materials, products and processes to the commercialization stage.
During the reporting year, TMK launched systematic collaboration with the Skolkovo Institute of Science and Technology in mechanics of materials, digital operations, digital twins, and the rollout of machine learning, machine vision, and predictive analytics technologies across TMK’s core production processes.
In 2020, TMK acted as an official partner of the Skolkovo Foundation in establishing and running Russia’s first accelerator for green technology startups, GreenTech Startup Booster, supported by the Russian Ministry of Natural Resources and Environment, Ministry of Construction, Housing and Utilities and Ministry of Energy. The project selected pilot projects offering innovative solutions for effective monitoring, reduction of per unit environmental impacts and integrated waste management.
TMK’s R&D facilities team up with specialized research organizations and universities in advancing experimental research across the following areas:
- Improving technologies to boost the economic efficiency of pipe and billet manufacturing, reduce production costs, enhance product performance, quality and appearance, improve working conditions and green operations;
- Ramping up new production capacity at TMK plants;
- Creating new technologies to manufacture new products;
- Deploying digital technologies;
- Improving the regulatory framework and technical documentation, developing national and corporate standards for pipe, billets, and flat-rolled products;
- Use of special steel grades to make products with specific properties;
- New threaded connections for drill pipe, casing and tubing for use in new hydrocarbon production technology applications.
In the reporting year, we developed, tested, and deployed a considerable number of innovative technologies and solutions:
- Corporate standards for products; state-of-the-art test methods;
- New types of pipe and threaded connections with improved reliability and strength, designed to develop unconventional hydrocarbon reserves;
- Rollout of new steel grades for pipe with increased resistance to sulfide corrosion cracking and local deformation for onshore and subsea pipelines;
- Expanding the product range of corrosion-resistant high-strength tubing and couplings made of complex alloy steel grades.
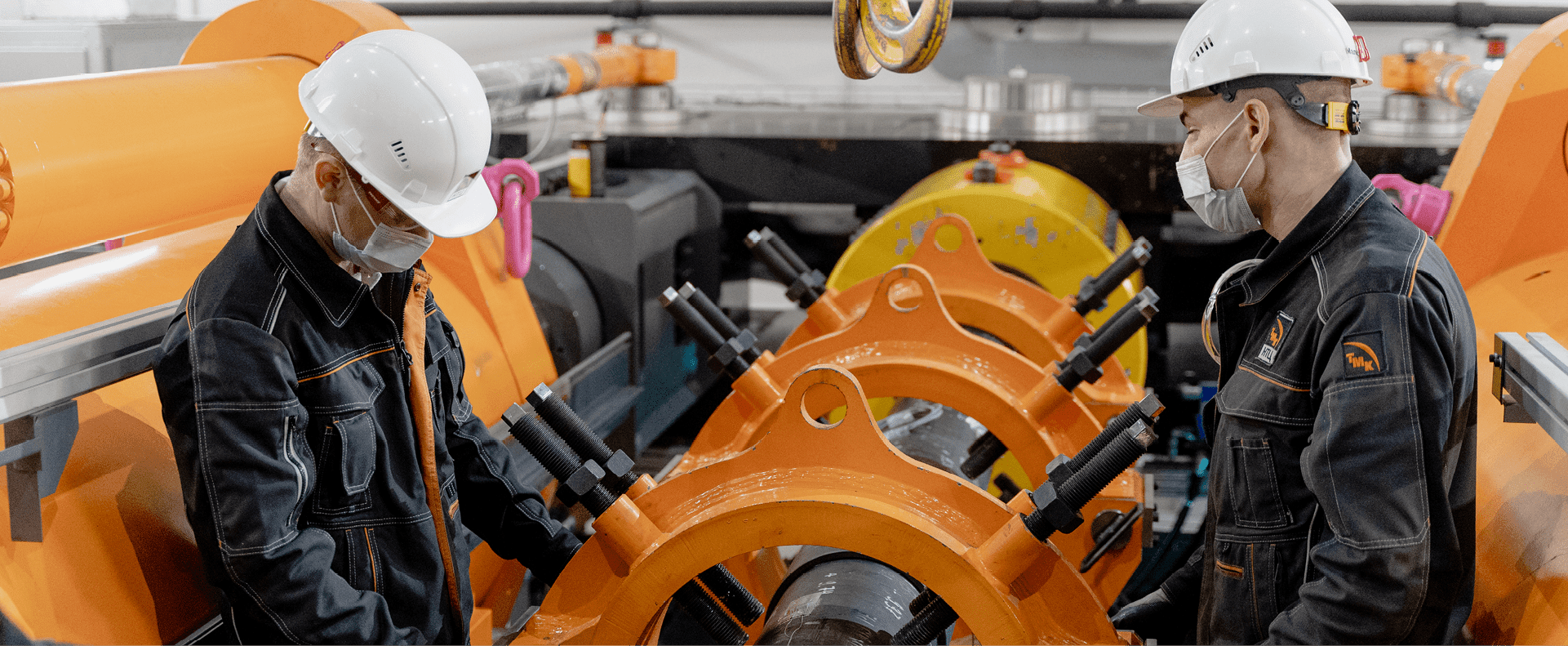
R&D Cooperation
TMK has a long history of successful collaboration with major consumers of tubular products through joint programmes for R&D cooperation.
Five R&D cooperation programs were implemented with Gazprom between 1998 and 2020. As part of these programs, unique import-substituting products have been rolled out to replace the imports that Gazprom previously sourced in markets abroad, such as CO2 service casing and tubing, TMK-C chrome and nickel alloy tubing, seamless and welded pipe for subsea pipelines, etc.
Under the joint R&D cooperation programme, TMK has committed itself to launching the production of import-substituting products within a set timeframe and at its own expense. These are advanced niche tubular products previously imported by Gazprom from abroad: pipes of special chromium-nickel alloys, of martensitic (13Cr and 13CrS — super chrome) grade steel, pipe with GREENWELL lubricant-free connections, as well as sour service pipe. The Company supplied 10,600 tonnes of these products to Gazprom subsidiaries over the contract period of
The format, content and toolkits of R&D cooperation programs are constantly evolving to match the objectives of customers. Today, along with the traditional R&D development program, TMK pursues joint projects with Gazprom under a long-term agreement providing for the serial production, deliveries, as well as maintenance, service and repair of import-substituting products against guaranteed supply volumes. A roadmap for the Smart Pipe project has also moved forward to build a gas pipeline monitoring system and roll out real-time controls for gas pipeline stress strain behavior and temperature.
Another example of the positive collaboration between TMK and Gazprom is the development of new product types to tap the Astrakhanskoye oil and gas condensate field with high H2S and CO2 content. TMK launched the production and successfully delivered OCTG to LLC Gazprom Dobycha Astrakhan for the Astrakhanskoye oil and gas condensate field. A total of three new product types were rolled out under the project, two of which had not previously been commercially manufactured by TMK due to a lack of consumer interest in domestic products — T95SS-grade casing and 89 mm and 114 mm C90SS-grade tubing, both for sour service. In addition, the Company has launched the production of tubing from the unique TMK-C chrome and nickel alloy, which has a high chromium and nickel content, preventing pipe corrosion in extreme downhole conditions with the double impact of high concentrations of hydrogen sulfide and carbon dioxide.
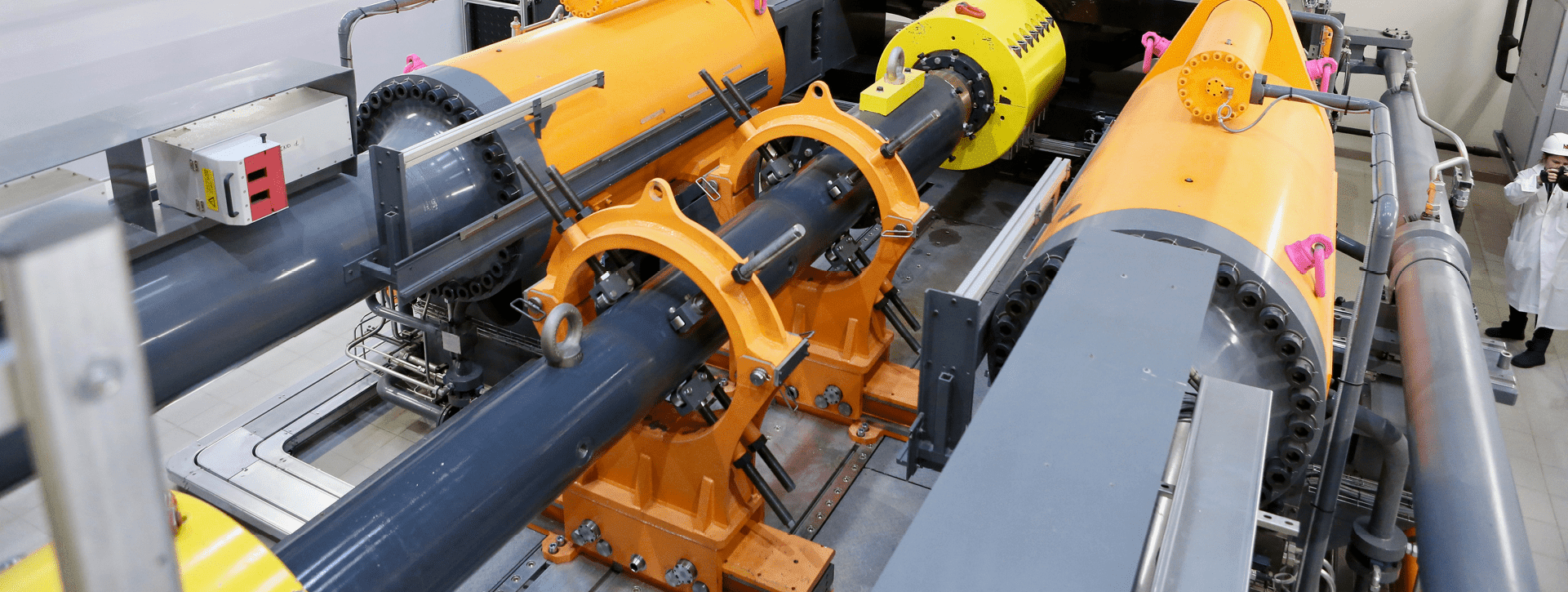
TMK is building relationships with other customers following a similar pattern. For example, special roadmaps are being implemented with Sakhalin Energy and Exxon Neftegas Limited, and a technology partnership model is being built with Gazprom Neft, providing for potential co-investment in agreed projects and challenges with further allocation of responsibility and benefits through special funds, startups and accelerators.
TMK has a long-standing partnership with Rosneft. TMK’s efforts under its five-year memorandum of understanding on cooperation in the implementation of the programme for import substitution of pipes for offshore projects were recognized in 2020 by a positive assessment from Rosneft representatives.
A new focus area for TMK is a cooperation agreement with State Atomic Energy Corporation Rosatom, in effect since 2019. Currently, 15 joint projects are advancing within the cooperation roadmap across eight areas of collaboration, such as the production and applications of high-tech tubular products, including development of new types of steel pipe, as well as R&D cooperation in developing new technical standards and R&D projects to create new steel grades.
As part of its cooperation with Rosatom, TMK is actively rolling out new types of high-tech tubular products in various sizes to meet the needs of the corporation’s enterprises. For example, unique pipes were developed for Rosatom’s mechanical engineering division for its BREST-OD-300 experimental demonstration power unit, which is to be built as part of the Technology Breakthrough project in Seversk, Tomsk Region. As part of a project to establish the closed nuclear fuel cycle, TMK will produce over 200 thousand meters of pipe to equip the steam generators of a fast neutron reactor.
TMK was the first company to successfully roll out in the shortest timeframe pipe products to meet the general technical requirements of Rosatom, to be used in all new NPP units with VVER reactors. The development of products to the new standards will reduce metal intensity of NPP equipment and significantly increase service life due to enhanced strength of pipework metal. The new standards will help standardize the product mix, as the standards are harmonized with the international ISO standard. TMK uses its co-chairmanship of Technical Committee 357 to actively promote, together with CNIITMASH, Rosatom’s modern requirements for the life cycle of NPP units — 60 years.
As part of its strategic goals of localizing the manufacture of gas production equipment in Russia, TMK has teamed up with Chepetsky Mechanical Plant, a Rosatom division, to launch the production of pipe made of TMK-C corrosion-resistant chrome-nickel alloy. Hot-deformed pipe produced by Volzhsky Pipe Plant is cold-rolled at Chepetsky Mechanical Plant, and the resulting cold-deformed pipes are passed on to Sinarsky Pipe Plant for threading gas-tight premium threaded connections developed by TMK. The 114 mm pipe resulting from this collaboration has been certified by PJSC Gazprom and will be supplied to its Astrakhanskoye gas condensate field, effectively replacing the imported counterparts purchased before.