ENERGY CONSUMPTION AND EFFICIENCY
Type of energy source | Unit of measurement | Consumption by volume | Consumption by value (RUB mln) | Consumption by volume | Consumption by value (RUB mln) | Consumption by volume | Consumption by value (RUB mln) |
---|---|---|---|---|---|---|---|
2018 | 2019 | 2020 | |||||
Natural gas | ths m3 | 708,793 | 3,188 | 678,922 | 3,136 | 661,658 | 3,117 |
Electricity | ths kWh | 3,148,077 | 9,515 | 3,073,858 | 10,080 | 2,899,829 | 9,943 |
Heat | Gcal | 1,046,475 | 1,477 | 945,478 | 1,420 | 894,020 | 1,431 |
Gasoline | tonnes | 202 | 10 | 241 | 12 | 230 | 12 |
Diesel fuel | tonnes | 3,089 | 136 | 3,605 | 165 | 3,286 | 153 |
Fuel oil | tonnes | 2 | 0.02 | 299 | 3 | 128 | 1 |
Total | 14,327 | 14,816 | 14,657 |
ENERGY EFFICIENCY
Improving the energy efficiency of operations is one of TMK’s key strategic objectives in ensuring the sustainable and cost effective use of natural resources and energy, reducing greenhouse gas emissions and increasing the competitiveness of its products.
The Company is implementing the Programme to Improve Energy Efficiency and Fuel and Energy Saving. All TMK plants are certified to ISO 50001:2011 international standard Energy management systems.
The energy savings achieved by initiatives aimed at reducing energy consumption across TMK operations and improving energy efficiency in
KEY INITIATIVES IMPLEMENTED AT TMK PLANTS IN 2020
Volzhsky Pipe Plant
- Increasing the electric arc furnace (EAF) power-off time during the hour intervals of working day capacity monitoring
- Reducing the overall heating and drying time for casting ladles due to reduced number of ladles
- Reducing the consumption of compressed air in the plant’s main shops by 3% by adjusting condensate drains and traps, timely repair of valves and elimination of pipe fissures
- Shifting heating of the EAF shop’s production areas to hot water supply
- Reducing oxygen consumption in the EAF shop by operating a single air separation unit
- Adjusting the nitrogen dosing mode in the EAF shop hopper
TAGMET
- Upgrading lighting systems, including the replacement of mercury-vapor and sodium-vapor lamps by LED lamps in the EAF, pipe rolling and pipewelding shops.
- Changing the operating modes of the EAF transformer
- Achieving fresh water savings of 200 thousand m3 through the use of process water in the chemical wastewater treatment unit and the use of blow-down water for desalination in the EAF shop’s water treatment units
Seversky Pipe Plant
- Reducing the cost of power capacity for Seversky Pipe Plant without changing the volume of electricity consumption by reducing the capacity of the electric arc furnace in the EAF shop during peak energy demand hours
- Optimizing the use of static VAR compensators Shutting down FKU-4 (harmonic filter) at Seversky Pipe Plant’s 220 kV substation during summer period
- Reducing the purchase price of natural gas for Seversky Pipe Plant’s industrial site through negotiations with the gas supplier
Orsky Machine Building Plant
- Using the existing modular gas-fired boiler house for process water heating instead of electric water heaters (gas cylinder production)
R&D facility’s building at the Skolkovo
TMK’s R&D facility’s building in Skolkovo earned international recognition for environmental and energy performance
TMK’s R&D facility’s building at the Skolkovo Innovation Centre received LEED Gold, a highly acclaimed international green building certificate, awarded by the U.S. Green Building Council (USGBC) following a multi-stage certification process.
TMK’s R&D facility in Skolkovo therefore became the 33rd LEED Gold certified building in Russia.
Leaders across the globe have made LEED (Leadership in Energy and Environmental Design) the most widely used green building rating system, which validates the most efficient and environmentally friendly methods of design and construction.
The R&D facility became the first LEED Gold certified building in Skolkovo, which hosts research centers of well-established Russian and international companies.
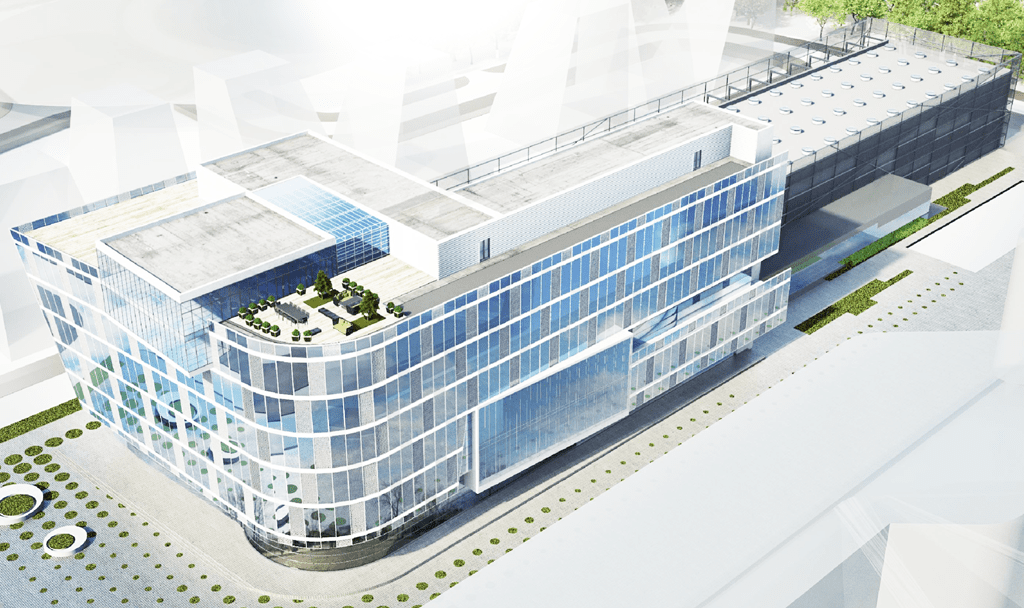