Capital Expenditures
In 2020, TMK Group’s expenditures on the acquisition of property, plant and equipment totaled RUB 10.5 billion (down 26% year-on-year). The Company adjusted the scope of its investment programme amid a challenging macroeconomic environment and prioritized projects aimed at expanding its OCTG and high value-added product manufacturing capacities, improving the reliability of heat supply and energy efficiency of operations, as well as reducing the environmental footprint of operations.
During the reporting year, TMK made a number of acquisitions worth a total of RUB 14.4 billion: acquisition of a 100% interest in LLC Parus metallurgical company (renamed to TMK — Yartsevsky Metzavod), as well as controlling stakes in several enterprises under LLC Truby 2000, one of Russia’s leading manufacturers of nuclear piping systems. The Companyalso increased its stake in the authorized capital of JSC Uralchermet, specializing in protective coating for pipes, to 75%.
Key projects completed under the Strategic Investment Programme in 2020
Volzhsky Pipe Plant
- The active implementation phase of the Technical Development of Pipe Rolling Shop No. 2 project was launched, aimed at increasing production of pipes from difficult-to-form steel grades and alloys to 55,000 tonnes per year
- The implementation of the environmental programme was continued — the construction of Hazard Class 4 to 5 landfill cell No. 8 at the landfill was completed
- ECO HOUSE TMK administrative and laboratory complex for the plant’s environmental function was launched. ECO HOUSE TMK features rooms for analytical monitoring of various environments — atmospheric air, natural, fresh and waste water, workplace air — as well as the assessment of human exposure to physical factors, and offices for employees. The environmental center is fitted with state-of-the-art equipment and high-precision measuring tools to support research
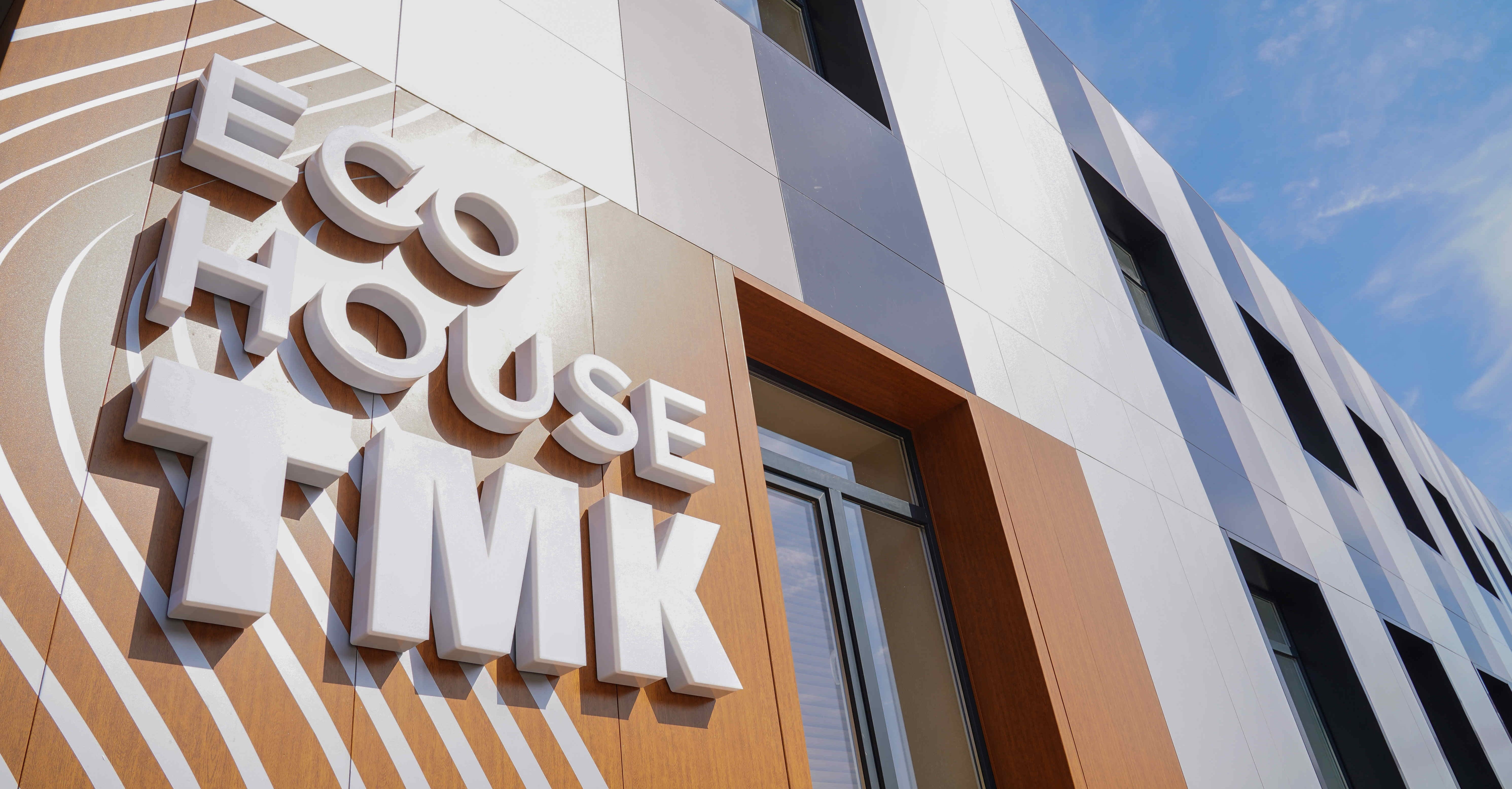
Seversky Pipe Plant
-
As part of a comprehensive revamp of the pipe-rolling facilities, the construction of a seamless pipe heat treatment facility was completed, and equipment with a capacity of up to 300,000 tonnes per year was put into operation. The technology and capacity are currently being ramped up.
The new integrated facilities were built through a partnership with RUSNANO under an agreement to upgrade Seversky Pipe Plant. The heat-treatment facility enables the Company to expand its production of premium products, providing oil and gas companies with pipes and threaded connections designed to operate in the most challenging climate and geological conditions. Pipe properties were improved by alloying and microalloying with nanostructure alloys which improved strength, ductility and corrosion resistance by 15% to 20%.
In addition to pipe heat treatment equipment, the new complex includes a water treatment facility with water recycling. A green technology deployed at the facility enables the reuse of 20 million m3 of treated water annually, significantly reducing the plant’s environment footprint, since the share of recycled water is 98.5%
- MAPEKO vertical casting ladle preheater for drying was put into operation as part of a comprehensive environmental program, which has significantly reduced the plant’s environmental footprint
TAGMET
- Pipe threading machines were commissioned in the pipe rolling shop, and the main pre-commissioning activities were completed for an electric arc furnace complex
- A project to upgrade the lighting systems of the EAF, pipe rolling and pipe-welding shops’ production areas was launched to reduce power consumption for the lighting needs of the plant’s main production shops by 85%. The project is scheduled for completion in 2021
Sinarsky Pipe Plant
- As part of the OCTG capacity expansion program, a press for hydraulic testing of OCTG was commissioned, and swedging equipment for pipes with TMK UP connections was put into operation
- The reconstruction project for Volochilnaya main step-down substation No. 3 was completed, enabling uninterrupted power supply to the plant’s main shops
TMK Oilfield Services’ entities
- As part of its casing pipe production line revamp project, TMK NGS-Buzuluk installed and commissioned a hydraulic testing system
- A CNC pipe threading machine was put into operation at the drill pipe repair facility of TMK NGS-Nizhnevartovsk
- Orsky Machine Building Plant put into operation a welding unit for tool joints
TMK’s R&D facility in Skolkovo
A number of contracts have been signed to purchase phase two core research equipment, with equipment deliveries ongoing. Currently the center is conducting comprehensive bench tests of premium OCTG connections to the standards of the International Organization for Standardization (ISO).
TMK-ARTROM
TMK-ARTROM carried out a comprehensive upgrade of the plant’s three shops: the rotary hearth furnace at the pipe rolling line was renovated, new pipe beveling machines were purchased, the cold-straightening machine was upgraded, the outlet section of the piercing mill was improved to increase the length of the rolled pipes, and the legacy pipe end trimming machines were replaced with new automatic positioning machines for high precision, high performance cutting of fixed lengths. In addition, a contract was signed in 2020 for the supply of new non-destructive ultrasonic testing equipment to detect defects across five areas: longitudinal, oblique and transverse defects, as well as pipe wall thickness and coating.
TMK-RESITA
TMK-RESITA overhauled components of the electric arc furnace, dust removal system and material handling equipment of the continuous casting machine. In 2020, a roof was installed over the hot slag pouring platform to reduce dust emissions as part of the plant’s environmental protection measures. In addition, an uninterruptible power supply system was purchased for the continuous casting machine, along with a cleaning machine for casting ladles, and a material feeding system was upgraded for the ladle furnace unit.